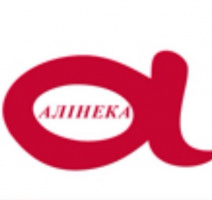
Внедрение новых технологий и оборудования в одной из отраслей промышленности, как правило, вызывает цепную реакцию разработки и освоения инноваций в соседних. Так, совершенствование конструкций горелок печных агрегатов для повышения эффективности сжигания топлива привело к существенному изменению теплотехнических режимов в топке (повышение температуры, увеличение скорости газового потока и агрессивности газовой среды). А это в свою очередь потребовало создания новых видов футеровочных материалов, которые отличаются от известных повышенными термомеханическими свойствами, определяющими долговечность топок котлов.
Комплексное решение задач повышения долговечности печных агрегатов, снижения трудозатрат на их возведение и ремонт обеспечиваются жаростойкими бетонами, обладающими высокими термомеханическими свойствами и позволяющими применять индустриальные методы изготовления футеровки. О них наша статья.
Горячая геометрия
В Украине традиционно для изготовления футеровки используют шамотный огнеупор в виде кирпича, кладку которого производят на жаростойкий раствор. Достоинствами этой технологии (применяемой с XIX века до сих пор!) являются сравнительная дешевизна и «мелкоштучность» строительных изделий: кирпич можно через люк подать в любую топочную камеру. Однако получаемое при этом ограждение имеет огромное количество швов, а различие в термическом расширении кирпича и растворных швов приводит к быстрому разрушению последних, ослаблению футеровки и необходимости ее частого ремонта.
Жизненный цикл конструкций топок сложной геометрии, построенных этим методом, еще короче. Практика свидетельствует, что хотя под теской и шлифовкой кирпичей можно уменьшить толщину швов, но скорое их разрушение неизбежно.
Кроме того, изготовление футеровки из мелкоштучных огнеупоров строго регламентируется технологией производства, что определяет потребность в высококвалифицированных рабочих. Это приводит к тому, что при относительно невысокой стоимости кирпича суммарные расходы на футеровку, определяемые упрощенно по схеме «цена материала + стоимость работ», высокие.
Поэтому на смену им идут гораздо менее трудоемкие в изготовлении футеровки из жаростойких бетонов, которые к тому же обладают по сравнению с распространенным огнеупором марки «ША» более высокими термомеханическими характеристиками. Прочность их в среднем выше в 2—4 раза, стойкость к агрессивной среде — выше на два порядка. А термическая стойкость бетонов вследствие их фрагментарной структуры выше этого показателя для шамотного кирпича в 3,7—4,6 раза.
Еще одной важной особенностью бетонов являются повышенные абразивные свойства, что в свою очередь увеличивает долговечность футеровки, особенно в тех случаях, когда технологией предусмотрены ударные и истирающие воздействия на стенки топок. Например, в печах шахтного типа для обжига извести, где шихта (известняк и кокс), опускаясь вниз по печи, разрушает футеровку из шамотного кирпича за один год.
Таким образом, более высокие по сравнению с шамотным огнеупором термомеханические и абразивные свойства жаростойких бетонов определяют их более высокую долговечность, а простота технологии изготовления футеровки (заливка в опалубку) — возможность быстрого сооружения относительно недорогого высококачественного ограждения в топках.
Пластические свойства жаростойких бетонов позволяют получить футеровку сложной геометрии, необходимую в амбразурах котлов и печей нефтепереработки, цилиндрических печах битумных установок, шахтных печах, пред-топах котлов, в дымовых трубах теплоэлектростанций — в любых теплоограждающих конструкциях.
Новейшая история
В конце 80-х — начале 90-х годов в Советском Союзе возводилось почти 300 000 м в год футеровки из жаростойких бетонов, что составляло около 10 % от необходимых строительных объемов. Сухие смеси для жаростойких бетонов выпускались на единственном в то время Радвилишском производственном объединении строительных материалов в Литве (годовой объем производства — всего 5000 т).
Низкий уровень производства и использования этих материалов объяснялся отсутствием специализированных предприятий по выпуску компонентов (цементов, высокотемпературных тонкомолотых добавок и заполнителей), а также несовершенством технологий их изготовления: нарушениями зернового состава и чистоты, применением цемента пониженной активности и т. д.
В 1996 году в Украине появились сухие смеси для получения жаростойких бетонов, разработанные киевской фирмой «АЛИНЕКА». До того времени наши теплоэнергетики могли только с завистью поглядывать на зарубежную продукцию, которая была и остается им не по карману (стоимость 1 т зарубежных сухих смесей — $5—20 тыс.).
Долговременная огневая точка
Известно, что в наиболее сложных условиях эксплуатируются горелочные устройства шахтных печей, смотровые амбразуры котлов и топки битумных установок. Это и высокие температуры, и термоудары, и коррозионное воздействие газовой среды (особенно при использовании мазутов, богатых сернистыми включениями). Время — лучший из испытателей — показало, что жаростойкие бетоны, полученные из отечественных сухих смесей, успешно противостоят этим постоянно возникающим в топке микрокатаклизмам.
Например, первая топочная амбразура, изготовленная в 1996 году на Дрогобычском НПЗ по монолитной технологии, эксплуатируется до сих пор. По этой же технологии изготовлены амбразуры печей на Сквирском комбинате хлебопродуктов, Немировском, Бершадьском, Степановском, Николаевском, Ракитнянском сахарных заводах, ООО «Зерноторговой компании», Одесском НПЗ, Киевском ДСК-3, Кировоградском, Мелитопольском, Винницком маслоэкстракционных заводах. На Дрогобычском НПЗ топка битумной установки до 1997 года была футерована огнеупором «ША» и останавливалась на текущий ремонт после каждых двух месяцев эксплуатации. После его замены на жаростойкий бетон установка работает уже четыре года без ремонтов. По монолитной технологии отремонтирована и битумная установка Киевского облавтодора.
Как правило, футеровка шахтной печи выполняется из доменного огнеупора. В случае прогаров, возникающих при нарушении гранулометрии шихты, температура на поверхности футеровки достигает 1300—1400 °С, что приводит к ее оплавлению и разрушению. При этом для ремонта необходимо срывать вышележащие слои кладки, что приводит к разрушению кирпича, а следовательно, к его дополнительному расходу для восстановления снятых слоев, а также к дополнительным трудозатратам. Выбивание оплавленного огнеупора и установка нового кирпичного ограждения нецелесообразны еще и потому, что при этом нарушается категория кладки: толщина шва должна быть не более 1 мм, а сооружение новой огнеупорной стены обычно возможно только при увеличении швов, ослабляющих всю обмуровку, что может привести к ее обвалу.
Кроме того, шамотный кирпич характеризуется низкой абразивностью, вследствие чего износ футеровки, например, в печах обжига извести на сахарных заводах составляет 20—70 мм за сезон, что приводит к необходимости проведения в топках ежегодного капитального ремонта.
Пластические операции на топках
Если же отдельные прогары «залечивать» жаростойким бетоном, то в разборке вышележащих слоев необходимости нет. Нужно лишь очистить поверхность и забетонировать проблемное место методом скользящей опалубки. В этом случае не нарушается монолитность футеровки и восстанавливается первоначальная геометрия печи. Отметим, что технология работы с жаростойкими бетонами настолько проста, что предприятия, как правило изготавливали футеровку собственными силами, не привлекая специализированные организации, а лишь следуя инструкции изготовителя сухих смесей. При этом сроки ремонтных работ уменьшились в 2—3 раза так как для изготовления футеровки требуется только уложить приготовленный бетон в опалубку, а 50—90 % своей марочной прочности он достигает уже в первые сутки твердения, что уменьшает время возведения ограждения по сравнению с кладкой шамотным кирпичом, где время ожидания схватывания раствора значительно больше.
Высокие термомеханические свойства определяют долговечность ограждения: за пять лет экспериментов не обнаружено оплавлений футеровки, изготовленной из жаростойкого бетона, даже в случаях возникновения «козіа» и экстремальных повышений температуры в топке. Это подтверждено и при эксплуатации шахтных печей Корделевского, Кирнасовского, Ольховецкого, Бершадьского и Кагарлыкского сахарных заводов.
Монолит в ассортименте
Мировая практика футеровки печных агрегатов свидетельствует о безусловной победе «монолитной» технологии, основанной на применении жаростойких бетонов, над «кладочной». В течение последних десяти лет каждая из ведущих фирм-производителей цемента — Lochay (Финляндия), PLIB-RIKO (Австрия), ALKOA (США) и Lafarge refraktere (Франция) — производит за год около 200 тыс. т сухих смесей.
В нашей стране объемы их выписка намного меньше, но ассортимент отечественных материалов уже включает в себя 17 марок, а стоимость украинских сухих смесей в 7—10 раз ноке, чем аналогичных зарубежных составов. Так что постройка «вечного» очага, избавляющего от ремонтных и сопутствующих им проблем, сегодня доступна каждому предприятию.
Свойства по заказу
Владимир ЕГОРОВ, начальник отдела комплексной теплоэнергетикиЗАО «Оргпищепром»
Применение футеровки печных агрегатов, изготовленной по монолитной технологии из жаростойких бетонов, обеспечило качественный скачок в теплоэнергетике. Отказ от привычных мелкоштучных огнеупоров позволил нашему предприятию резко сократить сроки монтажа котельного оборудования на различных объектах, одновременно повысив его надежность. Кроме того, возможность регулировки термомеханических характеристик возводимых конструкций, предоставляемая разработчиком сухих смесей, открыла для нас широкие перспективы в движении к новым нетрадиционным областям внедрения. Например, только благодаря тому, что есть возможность заказывать и термическую, и абразивную стойкость футеровки под особенности режимов работы объекта, мы смогли создать, внедрить и гарантировать долговечность уникального оборудования для сжигания лузги гречихи в предтопках котлов Двуречанского элеватора (Харьковская область) и ЧП «ВАГ» (г. Алчевск, Луганской области).
Рецепт экономичности
Экономичность футеровки тепловых агрегатов жаростойкими бетонами, получаемыми из сухих смесей, определяется следующими факторами.
• Не требуется дорогостоящее специальное оборудование: достаточно бетоно-смесителя и глубинного вибратора.
• Уменьшение трудоемкости работ на 20—45 % при увеличении производительности труда в 1,5—3 раза приводит к ускорению сроков ремонта в 2—4 раза.
• Пластические свойства бетонной смеси позволяют изготавливать футеровку сложной геометрии без нарушения монолитности конструкции топки.
• Уменьшение материалоемкости и отходов материалов на 7 % за счет возможности порционного изготовления.
• Транспортные расходы сокращаются на 20—25 %, так как бетон получается на месте производства работ.
• Гибкость технологии позволяет в каждом конкретном случае в зависимости от условий эксплуатации внести изменения в рецептуру сухой смеси для получения требуемых свойств футеровки.